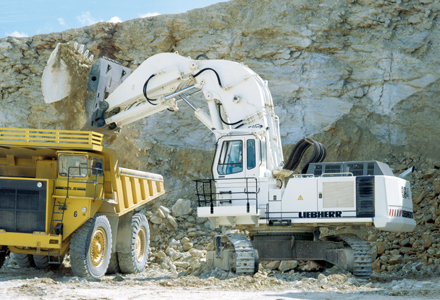
Europe appears to be split east against west as to whether front shovel or backhoe excavators are best for quarry applications. Claire Symes takes a look at the benefits of each approach
Choice of equipment in quarries is sometimes influenced by the layout and geology of the quarry, but in some cases the selection is dictated more by regional preferences. Large excavators seem to be a prime example - many Western European quarries favour backhoe (or backacting) excavators, while further east front loading shovel excavators are preferred.
The split seems to be based on historical preferences and continue mainly due to operator capabilities and maintenance experience. But what exactly are the benefits and disadvantages of each approach? "The choice of excavator also varies with geographic region - in Eastern and Central Europe front loading shovel excavators are more common but in Western Europe, backacting machines are dominant," said
"In the 1980s, anything over 100tonnes was a front shovel machine anywhere in Europe, but the trend has reversed in the last eight to 10 years and now 80% of machines are backactors." According to Edwards, part of the choice is familiarity and opting for equipment that can be easily maintained locally. "I was recently in an oil shale mine in Estonia that uses old Russian machinery and they like to stick to what they're used to," he said. "While in Bulgaria, I visited a quarry that prefers to operate four 250tonne electric front shovels rather than switch to modern backactors because the technology is simpler."
Dynamics
The advantage of a backhoe machine is that they pull material towards them and lift with the minimum radius so the lowest power and forces are needed. With a front shovel the opposite is true - they lift at the maximum radius. Not only is the energy use of a backactor lower but it also places less stress on the structure of the machine.
However,
"Front shovels work by pushing into the pile, away from the machine, but a backhoe pulls the material towards the superstructure and also exposes the bucket cylinder to damage. The breakout forces delivered by a front shovel are generally larger, which means it can operate with a larger bucket, offering higher production."
"Additional benefits include a better ability to load crushers; use a 'spike' to free lodged material from hoppers; work with a ripper to reduce, or eliminate blasting; more effective use of a hammer to reduce over-sized material."
Geology
Edwards added, "The geology of the quarry also has an influence on the advantages. When you blast, only around 15-20% of quarries will have a clean floor and in sites where the geology does not allow for this, the resulting toes will mean that the front loading shovel will only have a few points of contact on the tracks creating high stress. But a backacting machine sits on the blast pile giving it many more points of contact." Sinclair added that higher benches suit the face shovel but sites can usually be adapted to accommodate backhoe excavators if a different means of working the site is considered advantageous.
"The message that we are getting from quarry customers is that front shovels are slower,"
Size matters
"The size of excavator can be directly related to the output of a quarry," said Edwards "Quarries producing 500,000tonnes of aggregates a year would generally have a 52tonne machine, while one producing 750,000tonnes would need a 60 to 70tonne excavator and quarries with a million tonne output are likely to need an 80tonnes machine.
"But that is changing with the trend towards contractor loading and hauling. Many quarries are looking to operate for three months to produce enough aggregates for the full year using contractors. As a result the contractors are using 'over-sized' machines for the output of the quarry to meet this demand. This trend is stimulating demand for larger excavators.
"The disadvantage is that the quarries find it difficult to meet specialist orders but it is becoming more common in Western Europe." According to Elberskirche, one thing the customer is asking for more is a better fitting product. "We have expanded our range to meet this demand," he said.
"In Central and Southern Europe there is a trend for using 60-70tonne excavators and maybe a 45 to 50tonne machine for sorting, but in Germany they prefer smaller machines - in the 35 to 50tonne range. To meet this need we recently added a special mass excavation model in the 47tonne class."
Future power
"We are always looking for ways to further reduce the cost of ownership and one of the most recent developments to come out of this has been the regeneration of hydraulic energy to create faster cycle times with lower fuel costs," said Edwards.
"On a 90tonne machine, the older version used to use 75 to 80litres per hour but the newer one with regeneration, requires 65litres per hour. Customers have said that the savings go a long way to paying for the operator and some of the finance. But fuel consumption needs to be considered in terms of the fuel burn to tonne moved." Fuel costs are being brought sharply into focus with closer attention on operating costs and with the advent of Stage IIIB engine emissions regulations due in 2011.
"The next stage will bring new fuel requirements, as well as less fuel efficiency from having to run hotter to burn off the emissions, and maintenance costs will be higher with extra filtration," said Edwards. "The engines are likely to be very sensitive." Elberskirch added, "More technology is needed to meet the new regulations and everyone is taking a different approach but the diesel engine is still the preferred power unit.
"Hybrid power on quarry sized machines could happen but not yet. Battery technology is the main issue but the higher price - of around 30% for hybrid machines - is also a problem for customers.
"The technology works but more sophisticated batteries are needed for larger machines. But quarry machines will never become fully battery powered as some cars are because of the changes on the load of the engine required by different parts of the cycle."